How to turn plastic waste into profitable nanomaterials
Feb. 20, 2023.
4 mins. read.
3 Interactions
'Flash Joule’ technique efficiently turns would-be pollution into valuable nanomaterials
It would also be cool if the supply-chain/manufacturing-scale issues with nanotubes could be solved, and bring us into the next age of materials, with space habitats, invulnerable cars, etc.
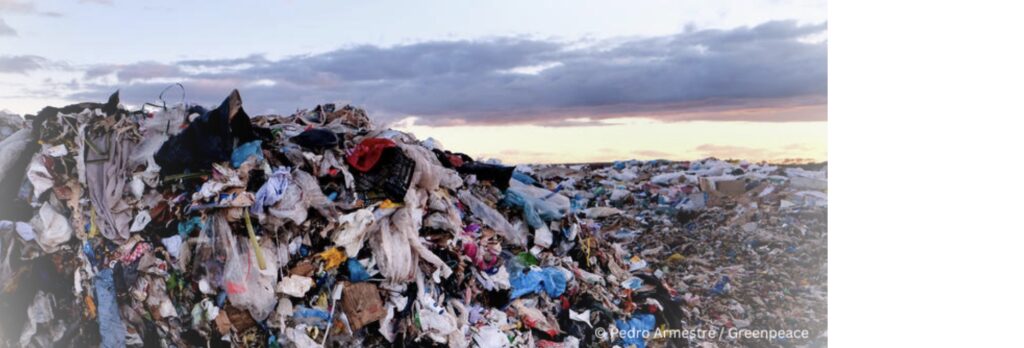
Plastic waste (credit: Organization for Economic Cooperation)
The amount of plastic waste produced globally has doubled over the past two decades and plastic production is expected to triple by 2050. Most of this waste is ending up in landfills, incinerated or otherwise mismanaged, according to the Organization for Economic Cooperation and Development.
When you put that soda bottle or takeout container into the recycling bin, you have no clue if it’s going to be converted into something new and useful. Some estimates suggest only 5% is actually being recycled.
Turning plastic into nanotubes and hybrid nanomaterials
Now Kevin Wyss, a Rice graduate student and lead author on a study published in Advanced Materials describes how he and colleagues in the lab of chemist James Tour had a solution. They used their flash Joule heating technique to turn plastic into valuable carbon nanotubes and hybrid nanomaterials.

By controlling the reaction parameters, a hybrid carbon nanomaterial consisting of nanotubes with graphene-sheet bits attached to their ends was obtained from mixed waste plastics. When used in composites, these hybrids performed better than either graphene or carbon nanotubes alone. (Credit: Tour lab/Rice University)
“We were able to make a hybrid carbon nanomaterial that outperformed both graphene and commercially available carbon nanotubes,” Wyss said.
Graphene, carbon nanotubes and other carbon-based nanomaterials are generally strong and chemically robust, have low density and lots of surface area, and possess conductivity and broadband electromagnetic absorption abilities. This makes them useful in a variety of industrial, medical and electronics applications such as composites, coatings, sensors, electrochemical energy storage and more.
The structure of the new hybrid carbon nanomaterial is responsible for its enhanced performance. “Let’s say I was trying to pull a string of yarn out of a sweater,” Wyss said. “If the string is straight and smooth, it can come out quite easily sometimes and ruin the weave. It’s the same with the carbon nanotubes; having these masses of graphene attached at the ends helps make them much harder to remove, thereby strengthening the composite.
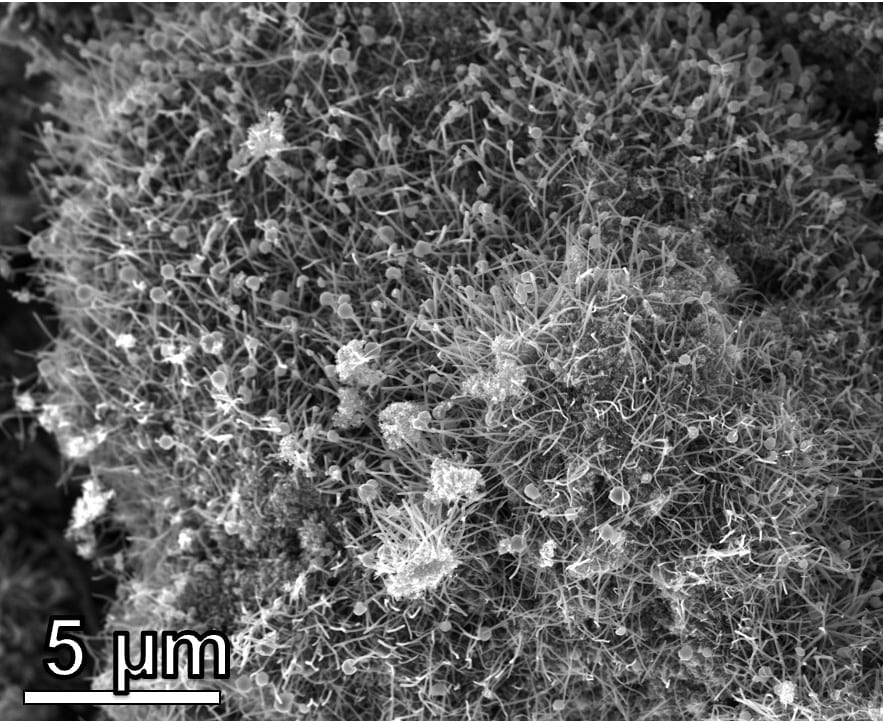
“Upcycling” for an economic incentive
“Recycling plastic costs more than just producing new plastic,” Wyss said. “There’s very little economic incentive to recycle plastic. That’s why we turned to upcycling, or turning low-value waste materials into something with a higher monetary or use value. If we can turn waste plastic into something more valuable, then people can make money off of being responsible in how they deal with discarded plastics.”
A life cycle analysis of the production process also revealed that flash joule heating was considerably more energy-efficient and environmentally friendly than existing nanotube production processes. “Compared to commercial methods for carbon nanotube production that are being used right now, ours uses about 90% less energy and generates 90%-94% less carbon dioxide,” Wyss said.
The plastic, which does not need to be sorted or washed as in traditional recycling, is “flashed” at temperatures over 3,100 kelvins (about 5,120 degrees Fahrenheit). “All we do is grind the material into small, confetti-sized pieces, add a bit of iron and mix in a small amount of a different carbon — say, charcoal — for conductivity,” Wyss said.
Machine learning
The researchers describe in Advanced Materials how machine-learning models that adapt to variables and show them how to optimize procedures are helping them push forward. “Machine-learning algorithms will be critical to making the flash process rapid and scalable without negatively affecting the graphene roduct’s properties,” said James Tour, the T. T. and W. F. Chao Professor of Chemistry and a professor of materials science and nanoengineering in Rice’s George R. Brown School of Engineering.
Citation: Waste Plastic into Hybrid Carbon Nanomaterials | Advanced Materials | DOI:
https://doi.org/10.1002/adma.202209621 Authors: Kevin Wyss, John Li, Paul Advincula, Ksenia Bets, Weiyin Chen, Lucas Eddy, Karla Silva, Jacob Beckham, Jinhang Chen, Wei Meng, Bing Deng, Satish Nagarajaiah, Boris Yakobson and James Tour.
Let us know your thoughts! Sign up for a Mindplex account now, join our Telegram, or follow us on Twitter.
0 Comments
0 thoughts on “How to turn plastic waste into profitable nanomaterials”